The future of 3D printing in manufacturing
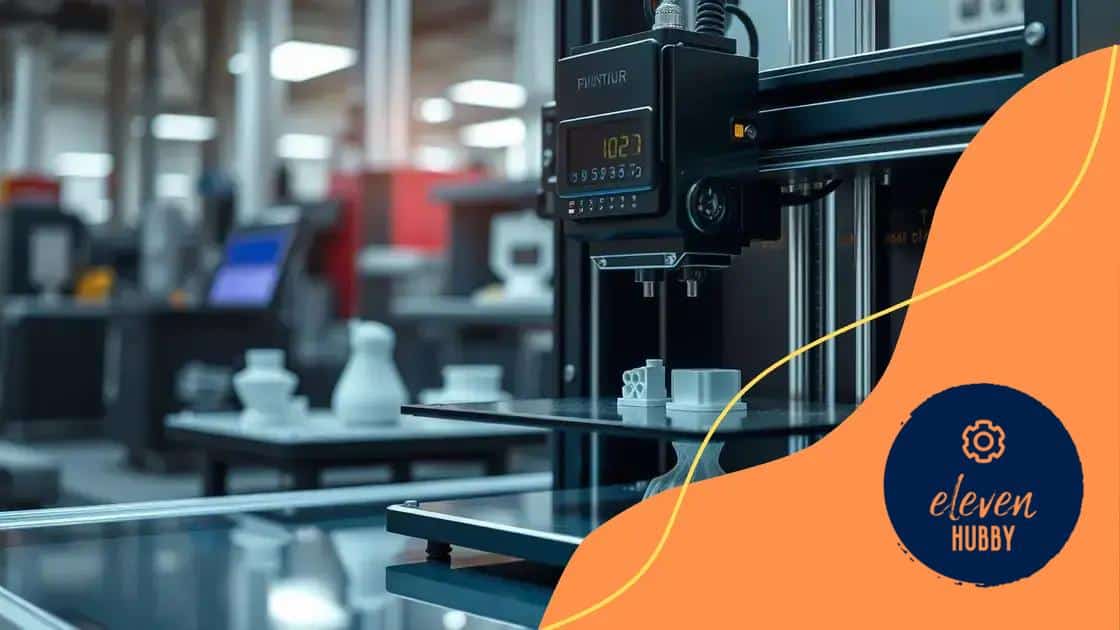
The future of 3D printing in manufacturing includes benefits like cost savings, design flexibility, and faster production, while facing challenges such as material limitations and regulatory compliance.
The future of 3D printing in manufacturing opens up exciting possibilities for industries looking to innovate. Have you wondered how this technology can reshape production and design? In this article, we’ll delve into the transformative impact of 3D printing and what it means for the future.
Understanding 3D printing technology
Understanding 3D printing technology is crucial as it reshapes industries. This technology allows for the creation of parts and models from digital files. It empowers manufacturers to produce complex structures that traditional methods struggle with.
The Basics of 3D Printing
3D printing, also known as additive manufacturing, works by laying down material layer by layer. This method offers unparalleled design freedom compared to conventional subtractive manufacturing.
- Cost-effective prototyping
- Customizable designs
- Reduced waste of materials
- Faster production process
The most common types of 3D printing technologies are Fused Deposition Modeling (FDM) and Stereolithography (SLA). FDM uses thermoplastics to create strong parts, while SLA works with photopolymers for smooth finishes.
Applications of 3D Printing
Various industries embrace 3D printing. For example, in healthcare, it aids in developing customized implants and prosthetics. In aerospace, it helps reduce weight while maintaining strength in components.
- Healthcare for custom implants
- Aerospace for lightweight components
- Automotive for prototypes and parts
Moreover, 3D printing enables rapid tooling, allowing manufacturers to quickly produce molds for injection molding. This accelerates product development and reduces time to market.
As you can see, understanding 3D printing technology provides insights into its potential. It revolutionizes the way products are designed and manufactured, leading to enhanced creativity and efficiency across various sectors.
Benefits of 3D printing in manufacturing
The benefits of 3D printing in manufacturing are driving innovation in various industries. This technology brings unique advantages that traditional manufacturing methods often cannot offer.
Cost Savings
One of the key benefits is cost savings. 3D printing reduces material waste by building objects layer by layer, meaning less leftover material. Additionally, it lowers production costs since companies can create prototypes quickly and without the need for expensive molds.
- Minimized manufacturing waste
- Lower prototyping costs
- Reduction in labor costs
Companies find that the initial investment in 3D printing technology pays off by streamlining production processes and cutting down on expenses.
Design Flexibility
Another advantage is design flexibility. Designers can create complex geometries that are impossible with traditional methods. With 3D printing, ideas can become products without the limitations imposed by conventional manufacturing techniques.
This flexibility allows for unique product customization. Businesses can easily modify designs to meet specific customer needs, enhancing satisfaction and increasing sales.
Faster Production
Speed is another critical benefit. 3D printing enables rapid prototyping and quicker iteration cycles. This speed allows companies to bring products to market faster, gaining a competitive edge.
- Rapid prototyping
- Shorter lead times
- Immediate feedback on designs
Production timelines shrink significantly, allowing teams to innovate and adapt quickly to market demands.
As manufacturers embrace these benefits, 3D printing technology continues to expand, fostering creativity and efficiency within the industry.
Applications across different industries
The applications of 3D printing across different industries are vast and transformative. This technology is changing how products are made and improving efficiency.
Healthcare Innovations
In the healthcare sector, 3D printing plays a crucial role. It allows for the creation of custom implants and prosthetics that match a patient’s unique anatomy. Surgeons can use printed models to plan complex surgeries, enhancing precision and outcomes.
- Personalized implants
- Surgical models for planning
- Customized dental applications
These innovations not only improve patient care but also reduce costs and recovery times.
Aerospace and Automotive Advancements
3D printing is extensively used in aerospace and automotive industries. It enables manufacturers to produce lightweight parts that optimize fuel efficiency and performance. These sectors benefit from rapid prototyping, which allows quick adjustments to design and function.
- Complex aerospace components
- Prototyping for faster development
- Lightweight automotive parts
The ability to test and iterate designs rapidly leads to better products and shorter production cycles.
Consumer Products and Fashion
In consumer goods and fashion, 3D printing opens doors to customization. Customers can choose designs tailored to their preferences, leading to unique and personal products. This technology challenges traditional retail models, pushing brands to innovate.
From jewelry to home decor, manufacturers use 3D printing to create items that stand out in a crowded market.
As you explore the applications of 3D printing, it becomes clear how indispensable this technology is across various industries, driving change and encouraging creativity.
Challenges facing 3D printing adoption
The challenges facing 3D printing adoption are significant obstacles that industries must navigate to fully benefit from this technology. As more companies look to integrate 3D printing, understanding these challenges can help in developing effective strategies for implementation.
Material Limitations
One of the primary challenges is the range of materials available for 3D printing. While advancements are being made, many traditional manufacturing materials may not yet have suitable 3D printable versions. This limits the applications of 3D printing in certain industries.
- Limited material options
- High cost of specialized materials
- Variability in material properties
As a result, industries often face hurdles in achieving the desired properties in the final products.
Regulatory and Compliance Issues
Another significant challenge involves regulations and compliance. Industries such as aerospace and healthcare have strict guidelines that must be followed. Compliance with regulatory standards can be complex and time-consuming when incorporating 3D printing technology.
This can slow down the adoption process as companies work to ensure their products meet necessary safety and quality standards.
Technical Expertise and Skill Gaps
A lack of skilled workers can inhibit the successful integration of 3D printing. Many organizations face a talent gap in understanding how to operate 3D printers and design effective models for production. Then, training personnel or hiring new staff creates additional costs and delays.
- Need for specialized training programs
- Difficulty finding qualified professionals
- High learning curve for new technology
As industries strive to overcome these challenges, they can unlock the potential of 3D printing and drive innovation.
The future trends in 3D printing
The future trends in 3D printing indicate a rapidly evolving landscape full of innovation and opportunities. As technology advances, industries are adapting to harness the benefits of this transformative process.
Increased Material Options
One major trend is the development of new and improved materials for 3D printing. Researchers are working on diverse materials that offer enhanced strength, flexibility, and sustainability. These materials expand the possibilities for applications in various sectors.
- Biodegradable materials for environmentally friendly products
- Composite materials for added strength
- Metals and ceramics for industrial applications
As these materials become more accessible, the use of 3D printing will continue to grow.
Integration with Other Technologies
Another trend is the integration of 3D printing with other technologies, such as artificial intelligence (AI) and the Internet of Things (IoT). This combination enhances printing processes and opens new avenues for customization and efficiency.
Companies are starting to utilize AI for optimizing printer settings and designs, ensuring better quality and faster production.
Personalization and Mass Customization
As consumer demands for personalized products rise, 3D printing provides an ideal solution. Companies can create tailored products efficiently, from customized footwear to personalized jewelry. This shift toward mass customization means consumers can get products that fit their specific needs.
- Tailor-made products for individual customers
- Adjustable designs based on consumer feedback
- Flexible production runs that cater to specific projects
These trends highlight the potential of 3D printing to continue reshaping manufacturing, making it more responsive to market demands and technological advancements.
FAQ – Frequently Asked Questions about 3D Printing in Manufacturing
What are the main benefits of 3D printing in manufacturing?
3D printing offers cost savings, design flexibility, and faster production times, which can enhance overall efficiency and creativity.
What industries are currently using 3D printing?
Industries such as healthcare, aerospace, automotive, and consumer goods are actively using 3D printing for various applications.
What challenges do companies face when adopting 3D printing?
Common challenges include material limitations, regulatory compliance, and a lack of skilled workers trained in 3D printing technology.
What are the future trends for 3D printing?
The future trends include increased material options, integration with AI and IoT, and a focus on personalization and mass customization.